TECHNOLOGY
Laser Robot: What Are They and How Do They Work?
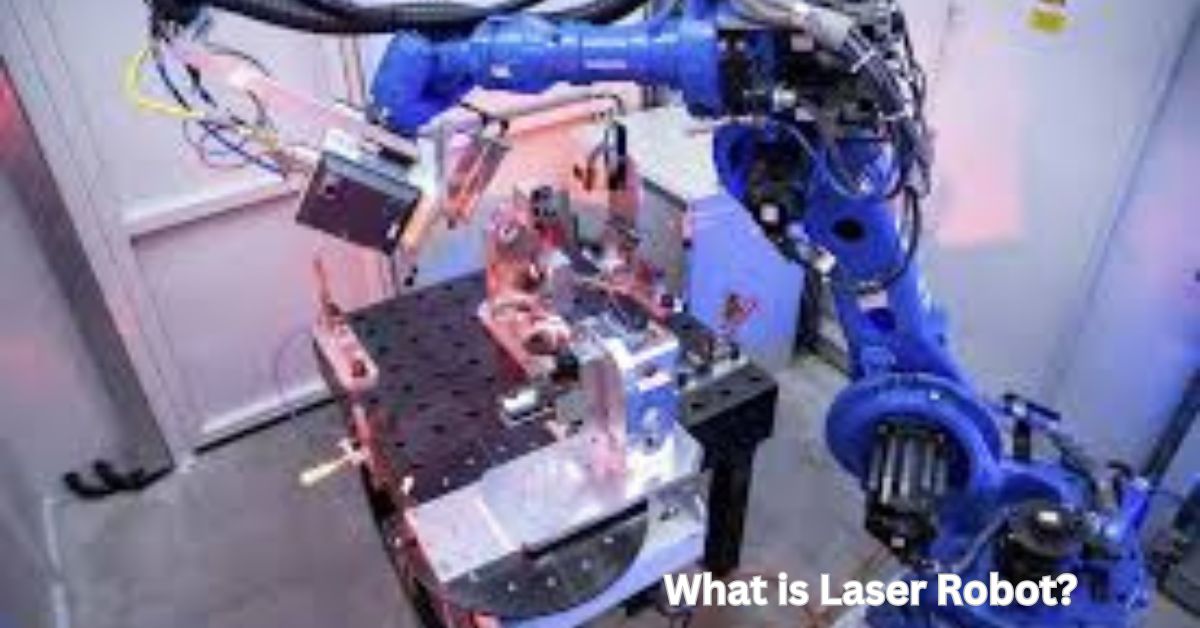
TECHNOLOGY
SEO Agency for Small Business Growth
TECHNOLOGY
Effortless Performance: Unlocking Power with Lenovo Drivers
TECHNOLOGY
iPhone Camera Not Working? Here’s What to Do Next
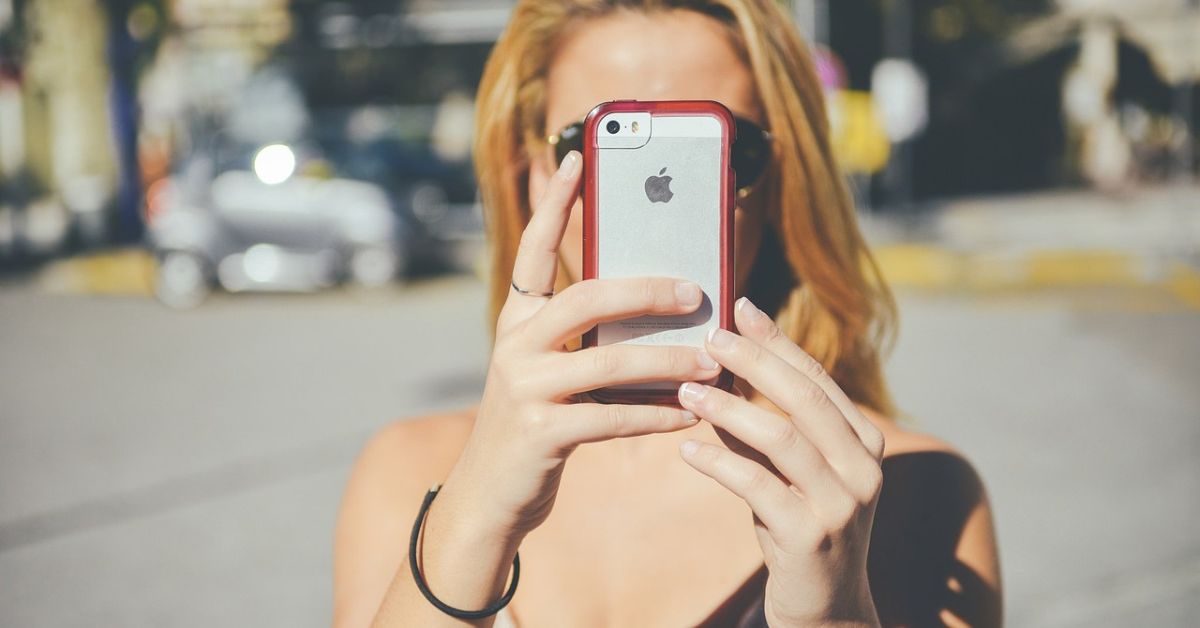
iPhone Camera Not Working? Here’s What to Do Next
Your iPhone’s camera is a vital tool for capturing life’s moments, whether it’s a family gathering, scenic sunset, or a quick selfie. However, encountering issues like the camera not working can be frustrating and disrupt your day. If you’re wondering why your iPhone camera suddenly stopped functioning or how to fix it, this guide will walk you through effective troubleshooting steps. We’ll explore causes such as software glitches, hardware problems, and settings misconfigurations, ensuring you can restore your device’s camera to full functionality.
Common Reasons Behind iPhone Camera Malfunctions
Software Glitches and System Bugs
One of the most common causes of a malfunctioning camera is a temporary software glitch. Whether it’s a frozen app, corrupted cache, or recent iOS update that introduced a bug, such issues can prevent the camera from launching or cause blurry images. System crashes may also affect camera performance.
Permissions and App Conflicts
Sometimes, the camera won’t work because apps don’t have the necessary permissions to access it. iOS has strict privacy controls, so if an app hasn’t been granted camera access, it may appear broken. Additionally, third-party camera apps or background processes can conflict with the default Camera app.
Hardware Damage or Faulty Components
Physical damage to the camera lens, sensor, or motherboard can cause the camera to malfunction. Dropping your phone or exposure to moisture can lead to hardware issues that software fixes cannot resolve. If the camera module is damaged, your iPhone might show a black screen or an error message when you open the camera app.
Storage Limitations
Insufficient storage space on your iPhone can indirectly affect the camera’s ability to save photos or videos, leading to freezing or crashing. If your device is nearly full, it may impact overall system performance, including the camera app.
Troubleshooting Steps to Fix Your iPhone Camera
Restart Your iPhone
The simplest and quickest fix for many issues is to restart your device. Powering off and turning your iPhone back on clears temporary glitches affecting the camera or system resources.
-
For iPhones with Face ID: Press and hold the side button and either volume button until the slider appears. Slide to power off.
-
For iPhones with a Home button: Press and hold the side or top button until the slider appears.
After restarting, test the camera app again.
Check for iOS Updates
Apple frequently releases updates that fix bugs and improve device stability. Running the latest version of iOS ensures your camera software is up-to-date.
Go to Settings > General > Software Update. If an update is available, download and install it. Afterward, try opening the camera app.
Verify Camera Permissions
Ensure the apps that require the camera have permission to access it.
Navigate to Settings > Privacy > Camera and confirm that the toggle is enabled for apps you use. If disabled, the app won’t be able to access the camera hardware.
Force Quit and Relaunch the Camera App
If the Camera app freezes or doesn’t open, force quitting and restarting it can help.
-
On iPhones with Face ID: Swipe up from the bottom and pause to open the app switcher. Swipe the Camera app off the screen.
-
On iPhones with a Home button: Double press the Home button and swipe away the Camera app.
Reopen the Camera app and check if it works properly.
Reset All Settings
Sometimes, misconfigured settings cause apps to malfunction. Resetting all settings will restore system preferences without deleting your data.
Go to Settings > General > Reset > Reset All Settings. You’ll need to re-enter Wi-Fi passwords and personalize preferences afterward.
Clear Storage Space
Check your available storage by visiting Settings > General > iPhone Storage. If storage is low, delete unused apps, old photos, or videos to free space and improve overall performance.
Advanced Fixes: When to Seek Professional Help
Hardware Diagnostics
If all software troubleshooting fails, hardware damage might be the culprit. Camera modules contain sensitive components, and a physical defect requires expert repair. You might notice symptoms like persistent black screens, blurry images, or camera app crashes.
Visiting an Apple Store or authorized repair center can help diagnose if your iPhone camera needs replacement or service.
Third-Party Repair Risks
Be cautious of unauthorized repair shops offering cheap fixes, as substandard parts or improper handling could worsen the issue or void warranties.
Preventative Tips for Your iPhone Camera
Use Protective Cases and Screen Guards
Protecting your iPhone from accidental drops or scratches is the first step to maintaining camera health. Cases with raised bezels shield the lens from direct impacts.
Avoid Excessive Moisture Exposure
Water and moisture can corrode internal parts and affect camera performance. Keep your phone dry and avoid using it in high-humidity environments.
Regularly Update iOS and Apps
Keeping your operating system and apps updated ensures you benefit from bug fixes and security patches that enhance camera stability.
Clean the Lens Gently
Sometimes blurry photos result from dirt or fingerprints on the lens. Use a microfiber cloth to clean the camera lens softly, avoiding harsh chemicals.
FAQs
Q: Why does my iPhone camera say it cannot connect?
A: This error usually indicates a hardware issue, often with the camera module itself. Restart your device first, but if the problem persists, consult Apple support.
Q: How do I fix a blurry iPhone camera?
A: Clean the lens gently and check for software updates. If photos remain blurry, the autofocus mechanism might be damaged.
Q: Can I use third-party camera apps if my default camera isn’t working?
A: Sometimes third-party apps can bypass minor issues, but if the hardware is faulty, these apps won’t work either.
Q: Why does the camera app crash immediately when I open it?
A: This is often due to a software glitch. Restart your iPhone, update iOS, and if needed, reset all settings.
Q: Is it safe to reset my iPhone to fix camera problems?
A: Resetting all settings is safe and won’t delete personal data, but a full factory reset erases all content—backup beforehand.
Conclusion
Facing an iPhone camera that isn’t working can be a major inconvenience, but most problems stem from software bugs or minor glitches that are relatively simple to fix. By systematically restarting your device, updating software, checking permissions, and managing storage, you can often restore your camera’s functionality without professional help. However, if hardware damage is the root cause, seeking authorized service is essential to avoid further complications. Keeping your device updated and protected will reduce the likelihood of future issues. With these tips, you’ll be ready to capture every moment with clarity and confidence again.
-
GENERAL6 months ago
Unveiling the 322 Messianic Prophecies: A Deep Dive
-
TECHNOLOGY6 months ago
What happened to spank bang
-
FASHION6 months ago
Debonair blog:The Art of Stylish Living
-
HEALTH4 months ago
Pure Clarity: The Power of Saline Contact Solution
-
ENTERTAINMENT6 months ago
What Is JerkMate? Exploring the Features and Purpose
-
FASHION6 months ago
Understanding the Carmelita Neck: A Unique Fashion Detail
-
ENTERTAINMENT6 months ago
Drake Exposed: The Untold Truth Behind the Music and Fame
-
BUSINESS6 months ago
Crypto FintechZoom: Navigating the Future of Digital Finance